Moulage sous vide des saumons Winglets
Par Ailes - Lien permanent

Ces moules ont été réalisés bénévolement par une équipe de constructeurs de Gazaile :
- Etude et traçage : JP GRIFFEUILLE, Louis MACABIAU, Frédéric MONFORTE
- Réalisation master : Frédéric MONFORTE
- Réalisation moules : Bernard MISSOL
Je les remercie grandement tant pour la qualité de leur travail que par l'esprit philanthropique qui les anime.




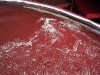

Merci à Charles Boulard d’avoir libérer les moules de saumons/winglets ULM samedi matin. J’ai pu tailler les différentes pièces l’après midi pour faire le sandwich : fibre verre 100gr/m², sergé carbone 200 gr/m², polystyrène extrudé de 3mm d’épais, fibre verre 200gr/m², tissus d’arrachage, film perforé, feutre buvard, bâche.





Comme Charles m’avait parlé d’une certaine difficulté à plaquer les plaques de polystyrène je les ai percées avec une aiguille tous les ~3 centimètres. De plus j’ai chanfreiné leurs bords pour faciliter le plaquage du dernier tissu de verre.
EDIT : Frederic Montforte recommande d'utiliser du Climapor de 2mm d'épais (chez Castorama) qui est micro-perforé plutôt que le Depron.


Le dimanche matin il pleut alors pas de VTT. Après une nouvelle lecture de la doc et des commentaires des autres utilisateurs je cire et lustre les moules. Je place le ruban adhésif sur le pourtour. Je décide de placer aussi le Sealtex : le mastique adhésif pour faire l’étanchéité de la bâche.


Je mets en place le compresseur sur lequel j’ajoute un bocal pour récupérer les éventuels suintement d’huile. J’en place un autre à l’entrée du circuit d’aspiration pour piéger les remontés de résine ou autres cochonneries. L'asservissement se fait par détection de la position de l'aiguille du manomètre à l'aide d'une fibre optique. Le moteur est directement alimenté par le capteur branché sur le 230Vac. Billet de la pompe à vide.



C’est l’après midi que je me lance dans le premier pot de résine pour environ 140gr. Il faudra un autre pot pour atteindre environ 280gr de SR1500/SD2503 par demi saumon (1.12kg au total).
Les plaques de polystyrène ne sont pas faciles à plaquer, même avec leurs trous quand la résine est bien fluide. Je lutte avec la dernière couche de fibre verre mais cela s’améliore quand on présente le tissu d’arrachage et les autres couches. N.B. : Pour cette raison les parties les plus faciles à faire sont celles de l’intrados.
Pour avancer rapidement j’ai planifié de faire toutes les parties dans la foulée. Le point bloquant est le système de vide. En effet je n’ai pas de nourrice pour faire un départ en étoile avec une branche par partie : l’idée est de faire un chaînage en série.


Pour la première partie pas de problème. J’ai fait le vide dans une bouteille de gaz (rouge) qui me sert de réserve. Du coup le peu de gaz qui restait propage une odeur bien caractéristique dans la maison…
Je mets un tuyau de la pompe vers le moule puis un autre du moule vers la bouteille de gaz. Je mets en marche le compresseur et j’ouvre la bouteille qui aspire un grand volume d’air. Cela permets de voir plus facilement où sont les fuites au joint de Sealtex et de les corriger. Quand tout est OK le manomètre descend à ~-0.76 bar et se stabilise.
Quand un autre moule est prêt, j’utilise une pince pour fermer de part et d’autre le circuit de vide. Cela me permet de débrancher la bouteille et d’insérer la nouvelle partie dans le circuit. J’utilise la réserve de la bouteille pour faire le vide dans le nouveau moule. Je pince le circuit entre le moule et la bouteille pour la déconnecter et la recharger au compresseur. Une fois ‘pleine’ de vide je la rebranche puis je reconnecte la chaîne au compresseur. Ainsi de suite pour les autres parties. La proximité des différents tuyaux et l’épaisseur du feutre propageant le vide d’un moule à l’autre.
Sur les photos on voit bien la remonté de résine à travers les trous des plaques de polystyrène.